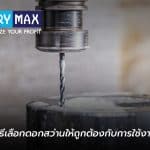
วิธีเลือกดอกสว่านให้ถูกต้องกับการใช้งาน
September 25, 2024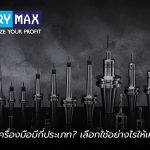
หัวจับเครื่องมือ (Tool Holder) มีกี่ประเภท เลือกใช้อย่างไรให้เหมาะสม
October 1, 2024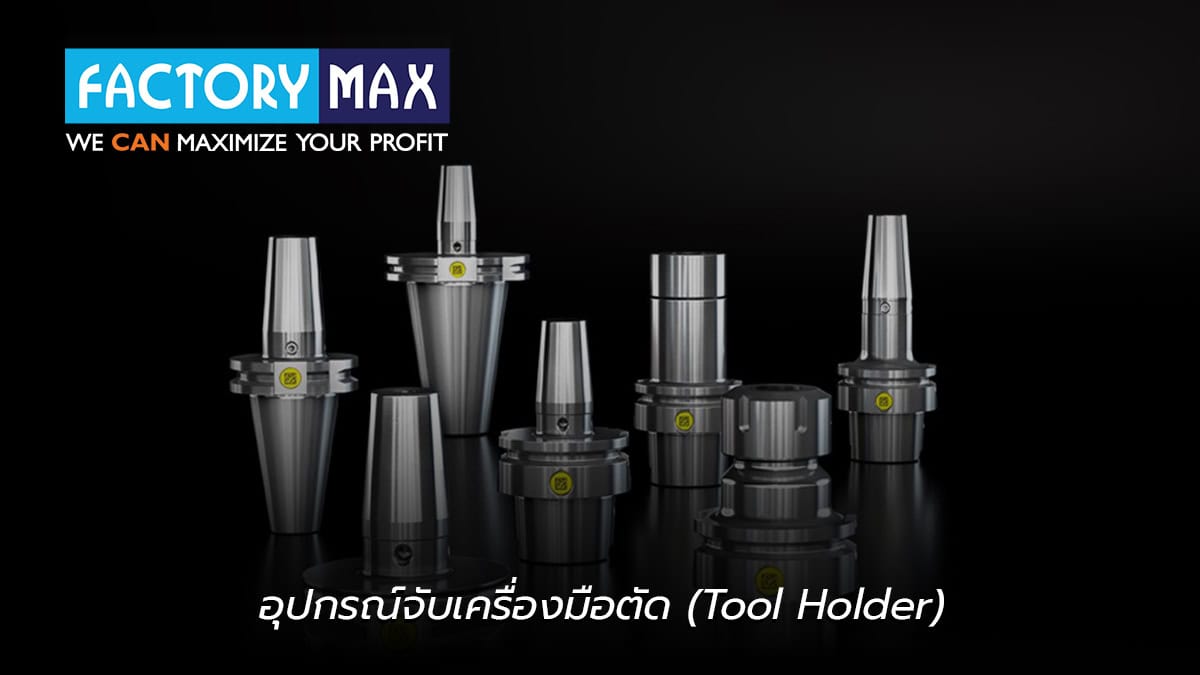
ในการใช้อุปกรณ์จับเครื่องมือตัดสำหรับเครื่องกัด (Tool Holder for Milling Machine) เช่น ดอกสว่าน หรือเอ็นมิลบนเครื่องกัด เราจำเป็นต้องใช้งานร่วมกับอุปกรณ์จับ ซึ่งมีอยู่หลากหลายประเภท ความเข้าใจอุปกรณ์จับแต่ละประเภทจะช่วยให้เราเลือกใช้งานให้เหมาะสม ทำให้สามารถผลิตงานได้ถูกต้อง รวดเร็ว มีความแม่นยำสูง อีกทั้งยังช่วยยืดอายุการใช้งานของอุปกรณ์จับ และเครื่องมือตัดให้ยาวนานขึ้น งานบางประเภทเราต้องการจับเครื่องมือตัดให้มีความเที่ยงตรงสูง บางประเภทต้องการจับยึดที่แข็งแรง หรือต้องการจับยึดเครื่องมือตัดที่ยาวๆ แต่อยากให้ลดการสะท้านของมีดตัด และชิ้นงานในขณะกัดงาน การเลือกใช้งานหัวตัดให้เหมาะสมก็จะแตกต่างกันไป
เลือกอ่านประเด็นที่สนใจ
- ประเภทของอุปกรณ์จับเครื่องมือตัดสำหรับเครื่องกัด
- หัวจับเทเปอร์ 7/24
- หัวจับแบบ HSK
- หัวจับแบบ BBT
- ความเร็วรอบสูงสุดของอุปกรณ์จับแต่ละประเภท
- ความสำคัญต่อประสิทธิภาพการตัดเฉือน
- การดูแลรักษาและใช้งานหัวจับให้มีอายุการใช้งานยาวนาน
หน้าที่ของอุปกรณ์จับเครื่องมือตัดที่ดีควรจะมีคุณลักษณะ ดังนี้
- จับยึดเครื่องมือตัดได้แข็งแรง รับแรงบิดได้สูง
- จับยึดเครื่องมือตัดได้แม่นยำเที่ยงตรง มีค่า Runout ต่ำ ๆ
- มีความแข็งแรงไม่โก่งงอ รับแรงกระทำที่เกิดจากการตัดเฉือนได้สูง
- มีความคล่องตัวในการจัดยึด และถอดเปลี่ยนเครื่องมือตัดได้สะดวก ทำงานได้ง่าย
- บำรุงรักษาง่าย ไม่เกิดสนิมกับอุปกรณ์จับได้ง่ายนัก
- มีผิวภายนอกที่แข็งไม่เกิดการเสียรูป หรือสึกหรอง่าย ซึ่งจะส่งผลต่อความแม่นยำในการจับยึดเครื่องมือตัด
- ไม่แตกเสียหายง่ายเมื่อเกิดการชน หรือการกระแทกจากการทำงาน
- รักษาความแม่นยำในการจับยึดเครื่องมือตัดได้ยาวนาน ไม่เกิดการล้าตัว หรือความเครียดจากแรงกระทำต่าง ๆ ที่เกิดจากการทำงาน ส่งผลทำให้อุปกรณ์จับเกิดการสูญเสียความแม่นยำในการจับยึดทูลไป การเสียรูปในเรื่องนี้จะเกิดจากกระบวนการผลิต และชุบแข็งของอุปกรณ์จับ
- มีผิวสัมผัสที่เรียบ ซึ่งจะช่วยให้การจับยึดเครื่องมือตัดมีความแม่นยำ
- การสมดุล (Balance) ของอุปกรณ์จับ ควรมีค่าต่ำ ๆ จะทำให้สามารถทำงานที่ความเร็วรอบสูง ๆ ได้ดี
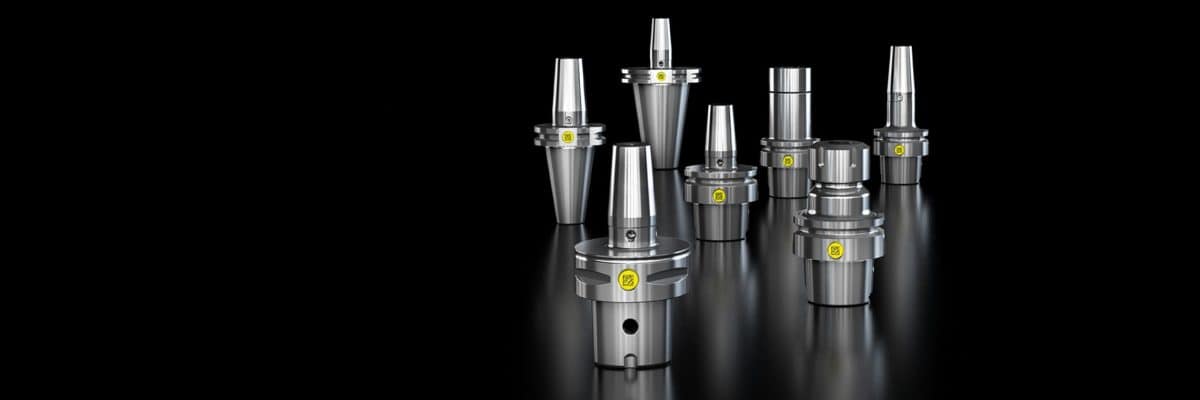
ประเภทของอุปกรณ์จับเครื่องมือตัดสำหรับเครื่องกัด (Type of Tool Holder for CNC Milling Machine)
1. หัวจับเทเปอร์ 7/24 (Taper 7/24)
เป็นทูล Taper7/24 ที่มีอัตราเรียว 7 ต่อความยาว 24 หน่วย ขนาดของอุปกรณ์จับในกลุ่มนี้ของแต่ละมาตรฐาน จะมีขนาดที่ใกล้เคียงกัน แต่แตกต่างในการออกแบบการจับยึดเข้ากับตัวเครื่องกัด หรือหัวสปินเดิล (Spindle) การใช้ตัวพูลล์สตัด (Pull Stud) และขนาดรูปทรงของการจับยึดตัวมีดกัด
- มาตรฐาน BT หรือ MAS
- มาตรฐาน SK หรือ DIN 169871
- มาตรฐาน DIN 2080
- มาตรฐาน ANSI B5.50 หรือ CAT
โดยมีขนาดที่ระบุถึงขนาดความโตของหัวจับที่นิยมใช้งานกัน 30, 40, 50 เช่น BT30, BT40, BT50
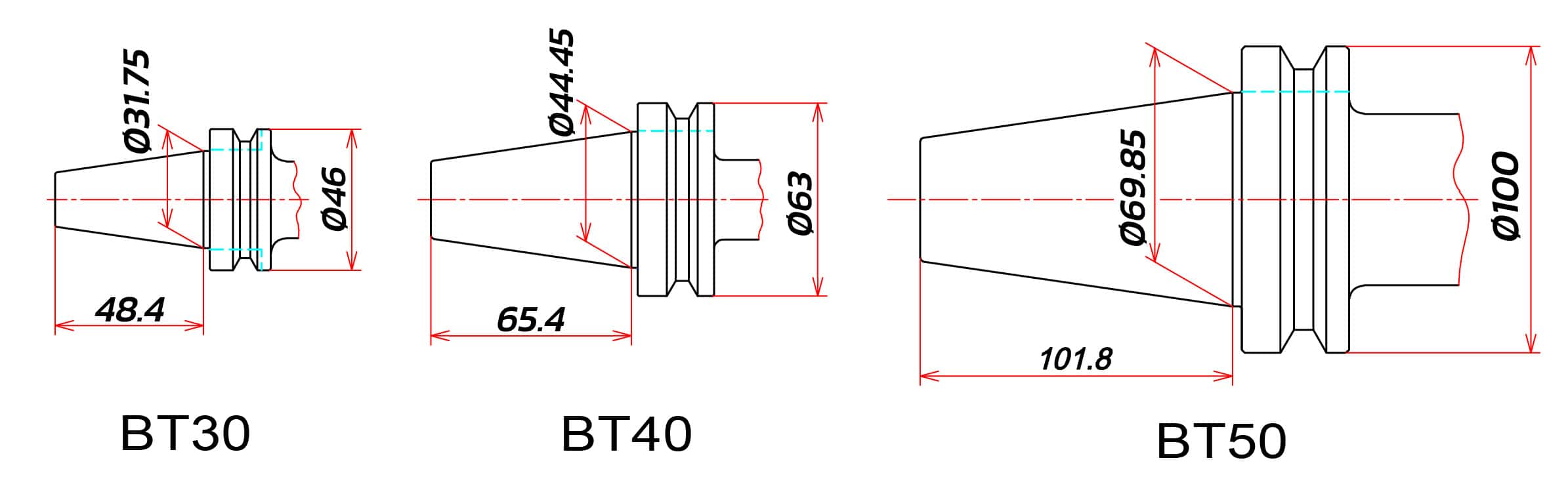
ภาพแสดงขนาดของอุปกรณ์จับ BT ตามขนาดต่างๆ
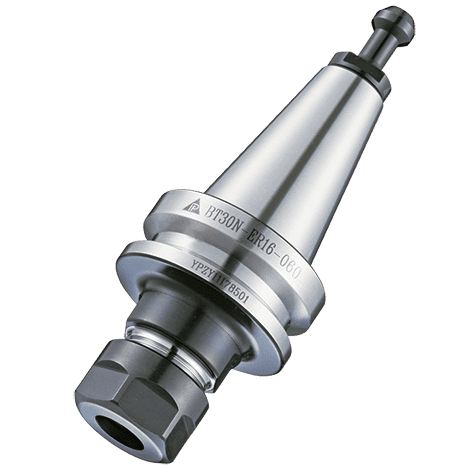
Parfaite CHUCK BT40
2. หัวจับผิวสัมผัสสองหน้า (Two Face Contact)
- มาตรฐาน HSK DIN69893 Type A, B, C, D, E, F มีขนาดให้เลือกใช้ ดังนี้ 25, 32, ,40, 50, 63, 80, 100, 125, 160 ที่นิยมใช้งานคือขนาด 40, 63 และ 100 ตัวอย่าง HSK-A63, HSK-C40
- มาตรฐาน BBT เป็นแบบ Taper 7/24 โดยมีการสัมผัสแบบ Two Face Contact ทางด้านหน้าเรียบด้วย
- เป็นแบบเฉพาะที่ผู้ผลิตหัวจับแต่ละเจ้าได้ผลิตขึ้นเฉพาะของตน และมีการจดสิทธิบัตร (Patent) ทำให้ผู้ผลิตรายอื่นไม่สามารถที่จะนำไปผลิตได้
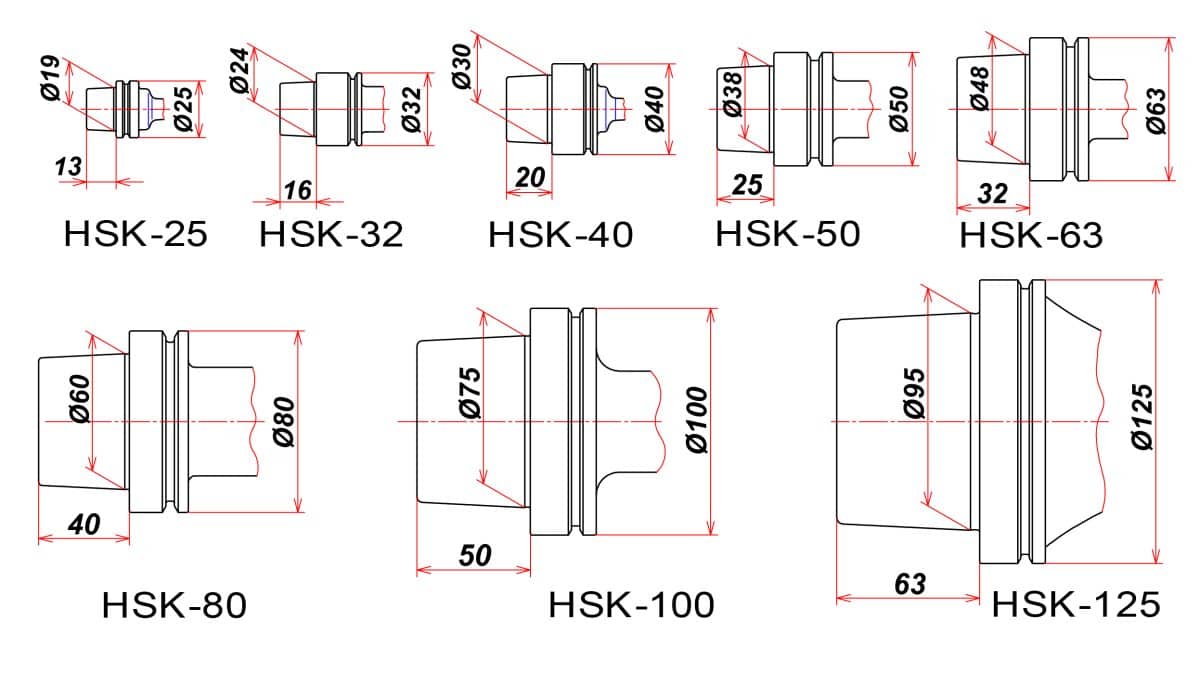
ภาพแสดงขนาดของอุปกรณ์จับ HSK ตามขนาดต่างๆ
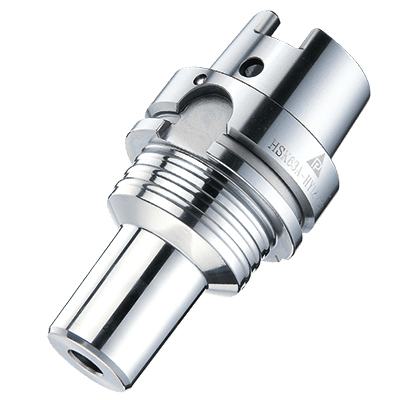
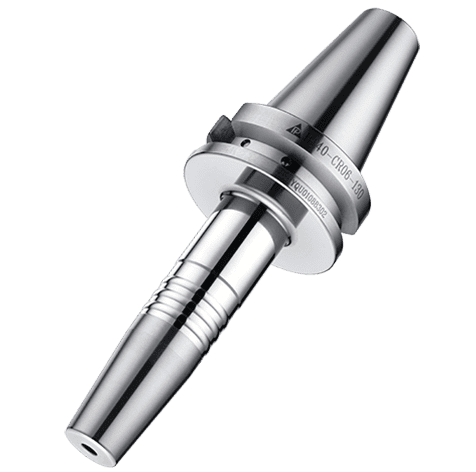
หัวจับเทเปอร์ 7/24
หัวจับเทเปอร์ 7/24 ได้พัฒนาขึ้นมาให้ทำงานกับเครื่องกัดในยุคแรก มีข้อดีคือแข็งแรง ส่งกำลังไปยังมีดกัดได้ดี ทำให้ทำงานหนักๆได้ดี แต่มีข้อด้อยในเรื่องความยาวของช่วงเทเปอร์ที่ค่อนข้างยาวมาก ทำให้เมื่อมีเศษสกปรก หรือการสวมเข้ากับเพลาขับ หรือตัวสปินเดิล (Spindle) จะเกิดความผิดพลาดได้ง่าย อีกทั้งเมื่อถูกแรงอัดในขณะทำงานจะเกิดการบิดตัวได้ จากการที่ไม่มีจุดรับแรงด้านหน้าของสปินเดิล อีกทั้งหัวจับแบบนี้ยังมีน้ำหนักมากทำให้ไม่สามารถทำงานที่รอบสูง ๆ ได้
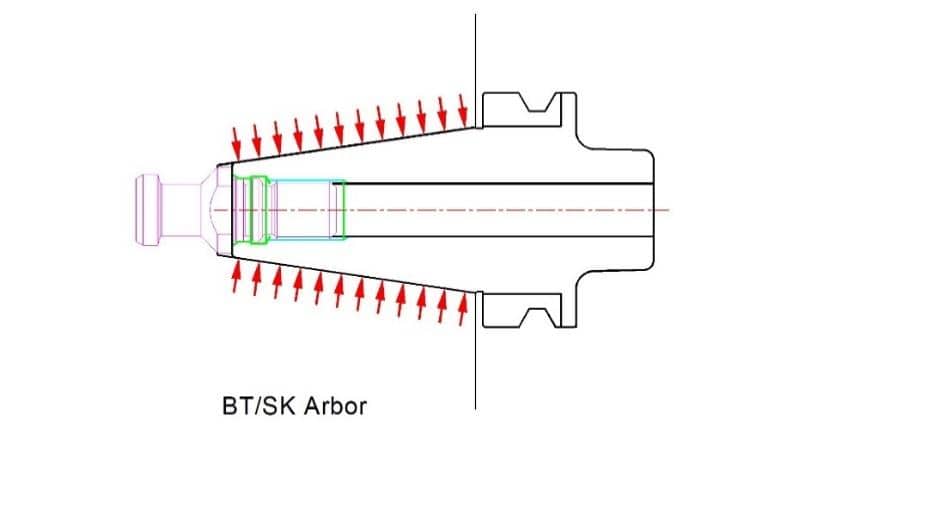
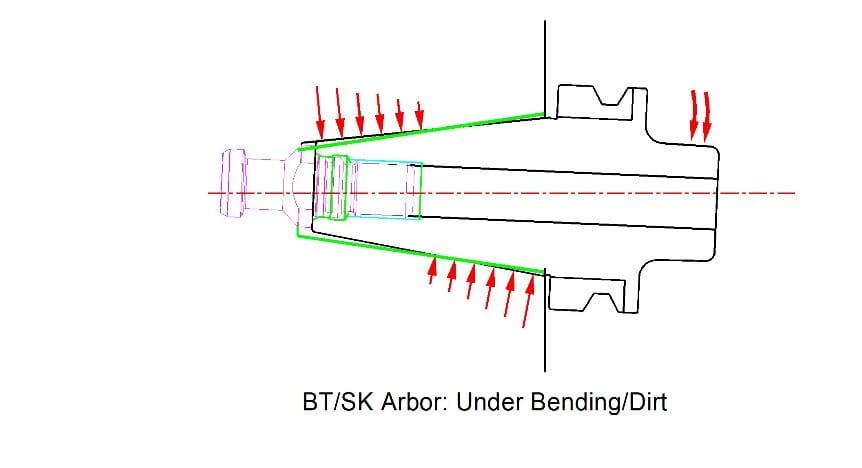
หัวจับแบบ HSK
หัวจับแบบ HSK หรือ DIN69893 จึงได้พัฒนาขึ้นมา โดยมีน้ำหนักที่เบากว่า สามารถใช้งานกับเครื่องจักรรอบสูงได้ดี ความยาวของเทเปอร์สั้น ทำให้การสวมเข้ากับสปินเดิลมีความแม่นยำมากกว่า มีผิวสัมผัสด้านหน้าช่วยรับแรงที่เกิดจากการทำงานได้ดี จึงทำให้หัวจับแบบ HSK นิยมนำมาใช้กับเครื่องจักรที่ต้องการรอบสูง ๆ หรือ HSM เป็นอย่างมาก
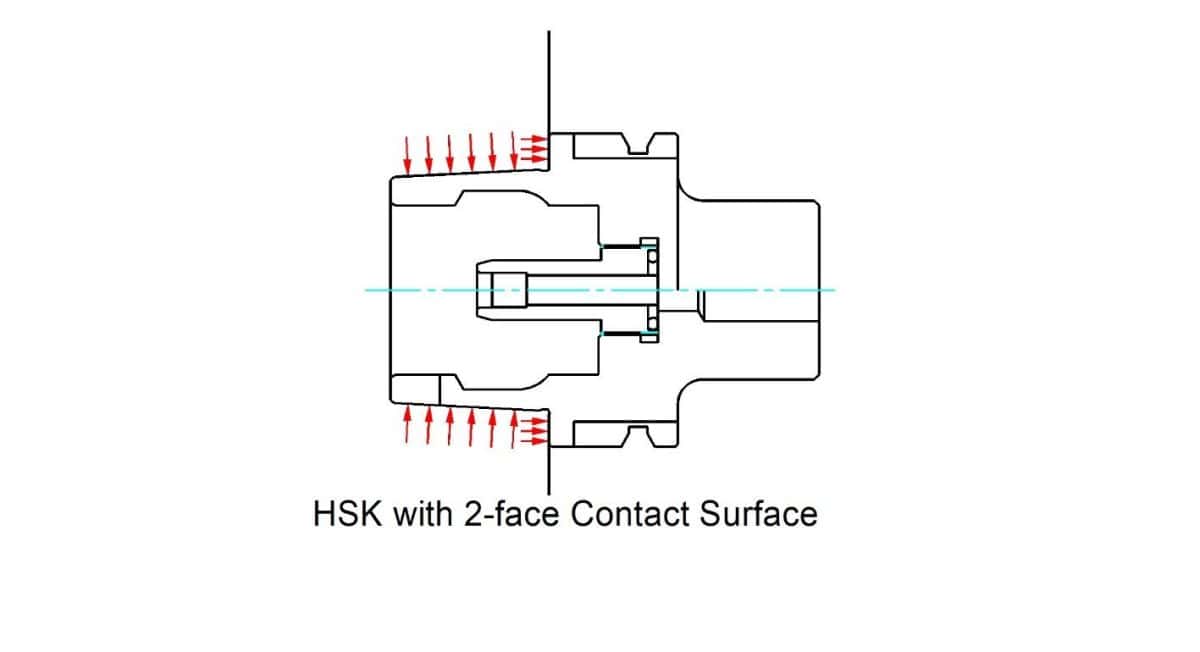
หัวจับแบบ BBT
หัวจับแบบ BBT หรือ BT-Two Face Contact เป็นหัวจับที่พัฒนาจาก BT พื้นฐาน ให้มีผิวสัมผัสด้านหน้าเพื่อช่วยในการรับแรงบิดจากการกัดงาน และมีการผลิตที่เที่ยงตรงกว่ารุ่น BT พื้นฐาน แต่ก็ยังมีข้อจำกัดเรื่องน้ำหนักที่สูงอยู่

ในการจับยึดหัวจับเทเปอร์ 7/24 จำเป็นต้องใช้ Pull Stud ซึ่งจะอยู่ที่ส่วนปลายด้านหลังของหัวจับ เครื่องจักรจะส่งแรงในการจับยึดมายัง Pull Stud เมื่อพิจารณาจากภาพจะเห็นว่าตำแหน่งดังกล่าวจะอยู่ห่างจากจุดกึ่งกลางของหัวจับเป็นอย่างมาก เมื่อเปรียบเทียบกับหัวจับ HSK ที่ใช้วิธีการยึด และส่งแรงมายังด้านในใกล้กับจุดกึ่งกลางของหัวจับ ทำให้หัวจับ HSK สามารถรับแรงได้ดีกว่าหัวจับเทเปอร์ 7/24 หรือหัวจับ BT อีกทั้งเมื่อไม่ต้องใช้ Pull Stud ในการจัดยึดก็จะทำให้การทำงานต่างๆ ลดความซับซ้อนลง
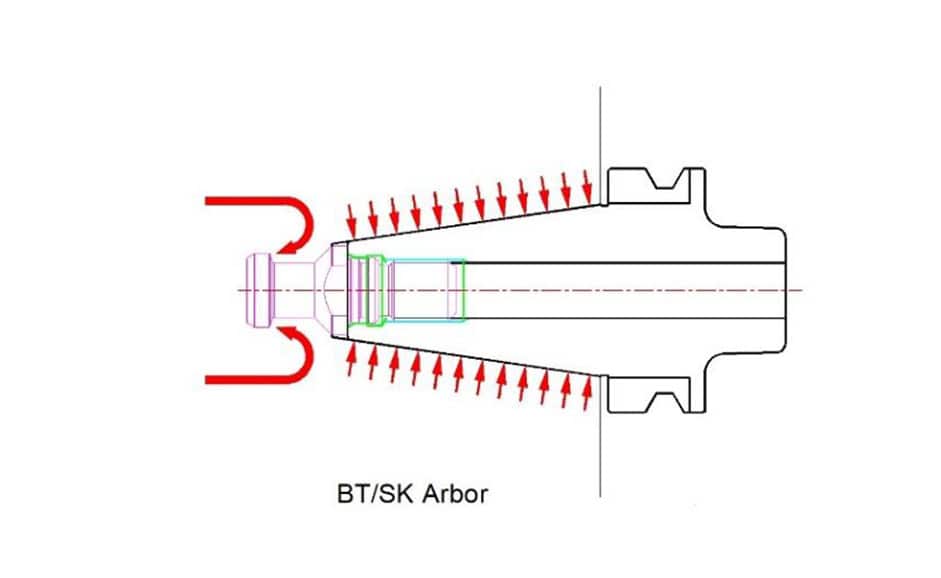
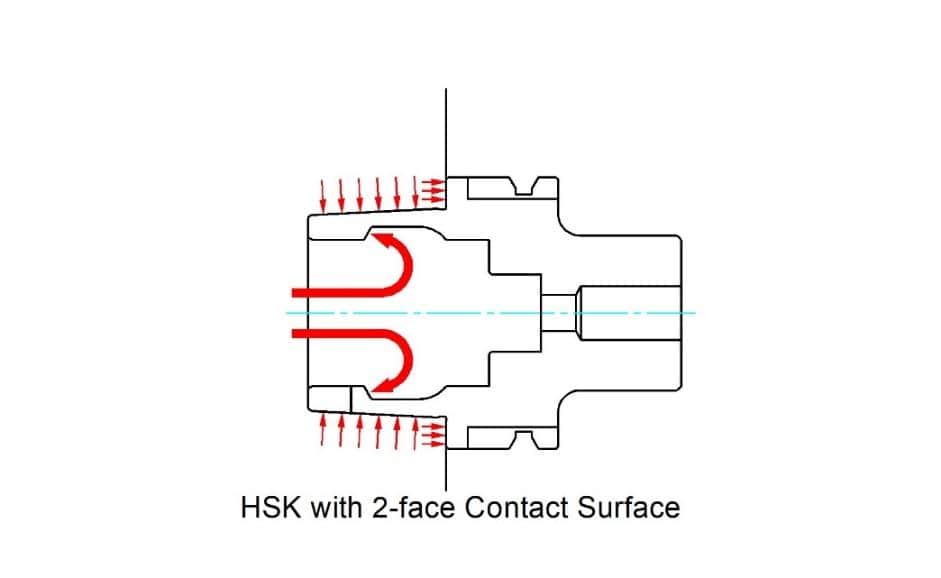
เทเปอร์ 7/24 (ISO, BT, SK, CAT) | HSK |
---|---|
– ค่า Stiffness ค่อนข้างต่ำ – มีความเที่ยงตรงในแนวแกนต่ำ – ไม่เหมาะกับงานความเร็วรอบสูง ๆ จากการล็อคที่อยู่ภายนอก – น้ำหนักมากและหัวจับมีความยาว – ใช้พื้นที่ทำงานที่กว้างกว่า HSK | – ค่า Stiffness ทั้งแบบสแตติกและไดนามิกที่ดีมาก – มีความเที่ยงตรงทั้งในแนวแกนและรัศมีที่ดีมาก – เหมาะกับงานความเร็วรอบสูง จากการล็อคที่อยู่ภายใน – น้ำหนักเบาและมีความยาวสั้น |
ความเร็วรอบสูงสุดของอุปกรณ์จับแต่ละประเภท
ความเร็วรอบสูงสุดที่สามารถใช้งานได้จะขึ้นอยู่กับน้ำหนัก และขนาดของอุปกรณ์จับเป็นสำคัญ รวมทั้งเรื่องการสมดุล (Balance) ของอุปกรณ์จับ อุปกรณ์จับที่ดีมีคุณภาพสูงจะมีการปรับค่าการสมดุล และตรวจสอบคุณภาพมาจากโรงงานผู้ผลิต ทำให้เมื่อใช้งานที่รอบสูง ๆ ช่วยลดแรงเหวี่ยงหนีศูนย์ที่จะเกิดขึ้นให้ต่ำลงได้ ส่งผลให้คุณภาพของงานมีความเที่ยงตรงขึ้น และไม่เกิดความเสียหายที่ส่งผลต่ออายุการใช้งานของเครื่องจักร
HSK Taper (Type A/C) | max rpm |
---|---|
25 | 60,000 |
32 | 50,000 |
40 | 42,000 |
50 | 30,000 |
63 | 25,000 |
80 | 20,000 |
100 | 16,000 |
Taper 7/24 (BT/SK) | max rpm |
---|---|
30 | 24,000 |
40 | 16,000 |
50 | 12,000 |
ตารางความเร็วรอบสูงสุดของอุปกรณ์จับแต่ละประเภท
การสมดุลหัวจับ (Balancing)
หัวจับควรมีการตรวจระดับคุณภาพการสมดุล ซึ่งกำหนดโดยค่า G จะขึ้นอยู่กับน้ำหนักของหัวจับ ระยะเยื้องของจุดศูนย์ถ่วงจากจุดศูนย์กลางกับความเร็วรอบที่ใช้งาน ซึ่งโดยทั่วไปควรมีค่า G6.3 ที่ความเร็วรอบ 25,000 รอบต่อนาที ถ้าเป็นหัวจับคุณภาพสูงควรได้ระดับคุณภาพ G2.5
อุปกรณ์จับเครื่องมือตัดที่ดีมีความสำคัญต่อประสิทธิภาพการตัดเฉือน
- วัสดุที่ใช้ทำหัวจับมีความแข็งสูง ไม่เกิดการสึกหรอ หรือเกิดรอยกดได้ง่าย
- มีค่า Runout ในการจับเครื่องมือน้อย ๆ
- จับงานได้มั่นคงแข็งแรงไม่คลายตัวได้ง่าย
- มีการสมดุลที่ดี (Balance) ทำให้ลดแรงเหวี่ยงหนีศูนย์ เมื่อทำงาน ที่รอบสูง ๆ
- การชุบแข็งที่เหมาะสม ถ้าหัวจับมีความหนาจะนิยมให้ที่ผิวนอกเป็นการชุบผิวแข็ง เพื่อให้ผิวด้านนอกมีความแข็งสูง ทนต่อแรงกดได้ดี ส่วนเนื้อวัสดุภายในมีความแข็งที่ต่ำกว่า (ที่ผิวนอกมีความแข็งประมาณ 60 HRC, ส่วนเนื้อในมีความแข็งประมาณ 30 HRC) ทำให้ทนทานต่อการแตกร้าว และรับภาระงานได้สูง กรณีที่ไม่สามารถชุบเฉพาะผิวแข็งได้หัวจับจะใช้การชุบแข็งทั้งชิ้นแต่ให้มีความแข็งที่ต่ำลงประมาณ 54 HRC
- มีผิวสัมผัสที่เรียบเงา มีความเรียบผิวต่ำ ๆ ทำให้ประกอบเข้ากับชิ้นส่วนอื่น ๆ ได้อย่างแม่นยำ
- รักษาขนาดความเที่ยงตรงได้ยาวนาน โดยกระบวนการผลิต และการชุบแข็งต้องทำให้เกิดความเค้นตกค้างในหัวจับต่ำ ๆ
- ใช้วัสดุที่ทนต่อการเกิดสนิมได้ยากกว่าเหล็กทั่วไป ทำให้ลดการดูแลรักษาลง