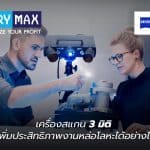
เครื่องสแกน 3 มิติ เพิ่มประสิทธิภาพงานหล่อโลหะได้อย่างไร
May 9, 2024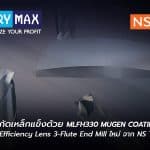
ลดเวลาการกัดเหล็กแข็งด้วย MLFH330 MUGEN COATING PREMIUM High-Efficiency Lens 3-Flute End Mill ใหม่จาก NS TOOL
June 14, 2024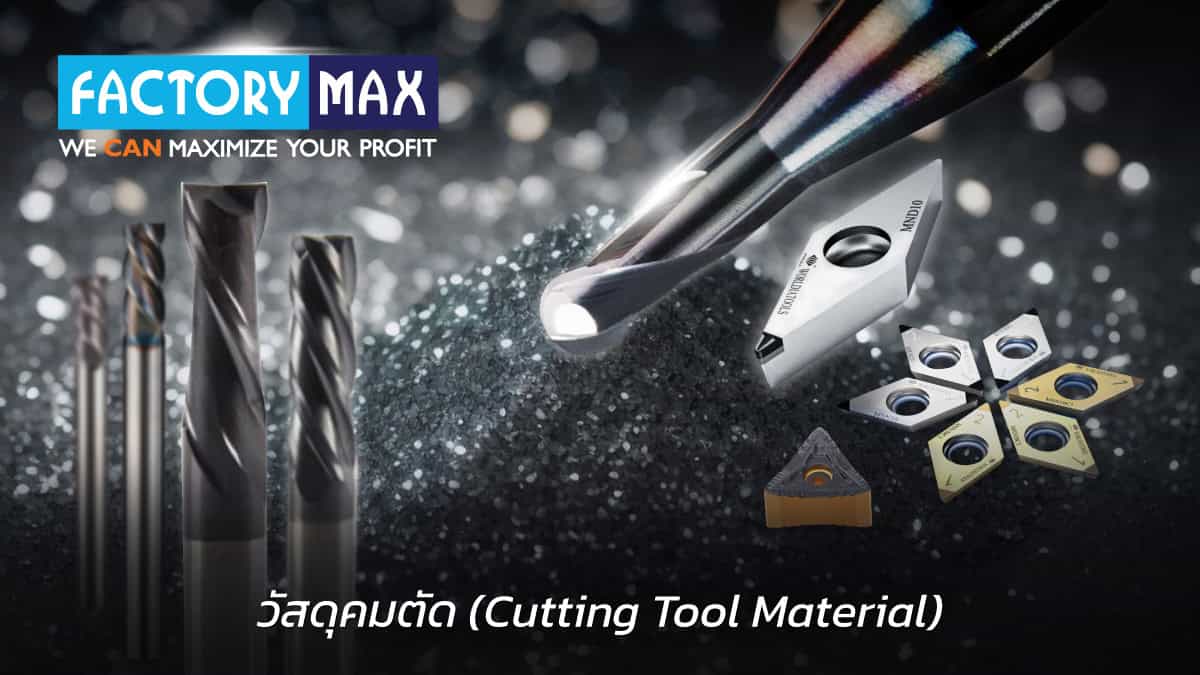
วัสดุที่นำมาใช้ทำเครื่องมือตัดในงานตัดเฉือนโลหะมีหลายประเภท ซึ่งมีสมบัติแตกต่างหรือใกล้เคียงกันในบางประเด็น การเลือกใช้งานวัสดุเครื่องมือตัดมีความสำคัญต่ออายุการใช้งานและประสิทธิภาพในการทำงานเป็นอย่างมาก
มีดตัดที่ดีต้องทนต่อการเสียรูปถาวรและทนต่อการสึกหรอได้ดี อีกทั้งยังต้องมีความเหนียว ไม่แตกหักง่ายเมื่อถูกแรงกระแทก และยังรักษาความแข็งไว้ได้เมื่อการตัดเฉือนมีอุณหภูมิสูงขึ้น นอกจากนี้ยังต้องสามารถผลิตเป็นมีดตัดตามรูปทรงที่ออกแบบได้ด้วยต้นทุนการผลิตที่ต่ำและเหมาะสมด้วย
การเลือกใช้วัสดุเครื่องมือตัด
- การทนต่อการขัดสี หรือมีความแข็งที่สูง
- การทนต่อความร้อน หรือการรักษาความแข็งของคมตัดที่อุณหภูมิสูงได้
- การทนต่อการแตกหักได้ดี หรือเป็นวัสดุที่มีความเหนียว (Toughness)
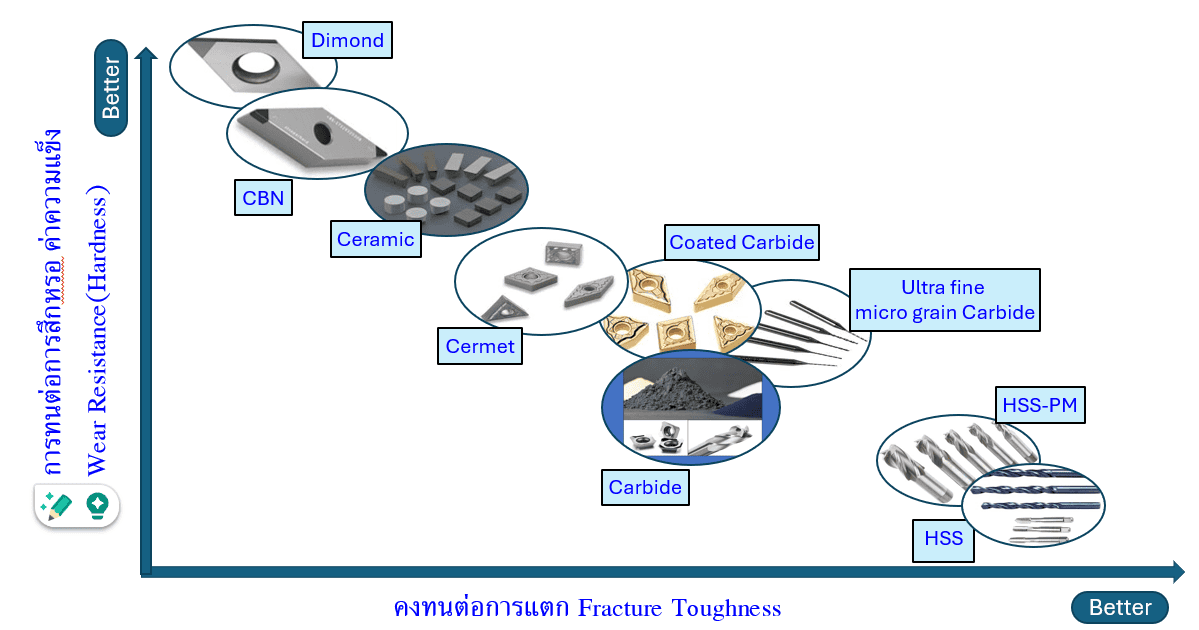
ประเภทวัสดุที่ใช้ทำเครื่องมือตัด
- เหล็กรอบสูงหรือ High Speed Steel (HSS)
- เหล็กรอบสูงชนิดผงโลหะ HSS-PM (Powdered Metal High-Speed Tool Steel)
- วัสดุหล่ออัลลอยโคบอลท์ (Cobalt-Based Alloy)
- ซีเมนต์คาร์ไบด์ (Cemented Carbided)
- เซอร์เมท (Cermet)
- เซรามิก (Ceramic)
- CBN (Cubic Boron Nitride Tool)
- เพชร (Diamond Tool)
การเลือกใช้วัสดุคมตัดมีองค์ประกอบตามลักษณะการใช้งานดังนี้
- ความแข็งและสมบัติเฉพาะของวัสดุชิ้นงาน วัสดุชิ้นงานที่มีความแข็งสูงก็ต้องการวัสดุมีดตัดที่มีความแข็งสูงขึ้นด้วย หรือวัสดุบางประเภทเกิดความร้อนสูงและต้านการตัดเฉือนได้ดี ก็จำเป็นต้องใช้วัสดุคมตัดที่ทนต่อความร้อน ทนต่อแรงกระทำ
- การทำงาน การเลือกใช้เครื่องมือตัดที่สามารถใช้ความเร็วตัดสูงๆ ได้ ทนต่อความร้อนได้ดี ส่งผลให้คุณภาพของผิวงานที่ดีขึ้น ลดขั้นตอนการทำงานลงได้ เช่นกลึงงานได้ผิวสำเร็จโดยไม่ต้องผ่านงานเจียระไน
- ปริมาณของเนื้อวัสดุที่ต้องทำการตัดเฉือนออกในปริมาณมาก ก็ต้องการวัสดุคมตัดที่ทำงานหนักๆ ได้ดี
- ความเที่ยงตรงด้านขนาดและผิวสำเร็จที่ต้องการ
- สภาพการทำงานเช่นแรงตัดเฉือน อุณหภูมิ ความสามารถและสภาพของเครื่องจักรที่ใช้ในการตัดเฉือน
- ความแข็งตรึง ( Rigidity ) หรือความมั่นคงของเครื่องมือตัดและชิ้นงาน เครื่องจักรหรือการจับยึดชิ้นงานที่มีความแข็งแรงต่ำ จำเป็นต้องใช้วัสดุมีดตัดที่มีความเหนียวสูงขึ้น ไม่เปราะแตกหักง่าย
- ความต้องการพื้นฐานในการผลิต ซึ่งมีผลต่อการใช้ความเร็วและอัตราป้อนตัดที่ใช้งาน
- ต้นทุนค่าเครื่องมือต่อชิ้นของงานที่นำมาผลิต รวมถึงต้นทุนค่าเครื่องมือ ต้นทุนงานเจีย อายุการใช้งานของเครื่องมือ ความถี่ในการลับคมใหม่หรือการเปลี่ยนมีดตัด และค่าแรงงาน โดยต้นทุนค่าใช้จ่ายในการผลิตที่ต่ำสุดอาจจะไม่ได้มาจากอายุการใช้งานของเครื่องมือตัดที่นานที่สุดหรือการลงทุนเริ่มต้นที่ต่ำที่สุดก็ได้
การเลือกแนวทางที่ดีต่องานตัดเฉือนทุกประเภท จะไม่เกิดจากวัสดุคมตัดเพียงอย่างเดียว เพราะว่าสภาพหรือเงื่อนไขการทำงานที่หลากหลาย วัสดุคมตัดแต่ละประเภทจะมีคุณสมบัติการทำงานได้ดีเฉพาะด้าน
1. เหล็กรอบสูง หรือ HSS
เหล็ก HSS เป็นเหล็กคาร์บอนผสมสูง และมีธาตุอื่นผสมอยู่ในปริมาณมากเช่น ทังสเตน โมลิบดินั่ม โครเมี่ยม เพื่อเพิ่มความแข็ง ความเหนียวและทนต่อการสึกหรอได้ดี เหล็ก HSS จะเริ่มสูญเสียความแข็ง เมื่ออุณหภูมิสูงเกิน 400 °C ดังนั้นในการตัดเฉือนเพื่อไม่ให้มีดตัดมีอุณหภูมิสูงจะต้องใช้น้ำหล่อเย็นเสมอ เพื่อช่วยยืดอายุการใช้งานของมีดตัดให้นานขึ้น วัสดุชนิดนี้สามารถนำไปลับคมตัดและนำกลับมาใช้งานใหม่ได้อีก สามารถนำมีดตัดไปเคลือบผิวเพื่อช่วยยืดอายุการใช้งานของคมตัดให้นานขึ้นได้
การใช้งานและสมบัติของวัสดุ HSS
- ช่วงความเร็วตัดใช้งาน 20-50 m/min
- อุณหภูมิการใช้งานไม่เกิน 400 °C
- ความแข็งของวัสดุ HSS ไม่เกิน 67 HRC
วัสดุ HSS ในปัจจุบันถือเป็นวัสดุคมตัดพื้นฐานที่มีการใช้งานกันแพร่หลาย แบ่งเป็น 3 กลุ่มใหญ่คือ
- กลุ่ม M มีโมลิบดีนัมเป็นสารเจือหลัก
- กลุ่ม T มีทังสเตนเป็นสารเจือหลัก
- กลุ่ม V วาเนเดียม (Vanadium) วัสดุในกลุ่มนี้จะคล้ายกับกลุ่ม T โดยเติมวาเนเดียมกับโคบอลต์เพิ่มขึ้นแล้วลดส่วนผสมของโมลิบดีนัม
วัสดุ HSS ที่ใช้งานกันทั่วไปจะมีความแข็งประมาณ 63 – 68 HRC แต่บางเกรดสามารถชุบแข็งได้สูงถึง 70 HRC มีดตัด HSS ที่ใช้งานความแข็งเกิน 68 HRC จะต้องระมัดระวังหรือมีเงื่อนไขในการทำงานที่เหมาะสม เพราะ HSS จะมีความเปราะสูงและแตกหักง่าย
วัสดุ HSS จะมีความเหนียวพอเพียงที่จะทนต่อแรงกระแทกได้ดี ทนต่อการกระแทกจากการตัดเฉือนที่ไม่ต่อเนื่อง (Interrupt Cutting) ได้ดีกว่าคาร์ไบด์ การเพิ่มความเหนียวของวัสดุ HSS สามารถทำได้ด้วยกระบวนการทางความร้อน ในกรรมวิธีชุบแข็งสามารถเลือกอุณหภูมิที่โครงสร้างทางจุลภาคมีเนื้อที่ละเอียดขึ้น ซึ่งก็จะทำให้วัสดุ HSS มีความเหนียวที่สูงขึ้น นอกจากนี้วัสดุ HSS จะเหมาะกับงานที่ต้องการความคมของมีดตัดสูงๆ อีกด้วย
ข้อจำกัดของวัสดุ HSS
- ปัญหาที่สำคัญของวัสดุ HSS ที่ผลิตด้วยกระบวนการหลอมคือ คาร์ไบด์เกิดจากจับตัวกัน แล้วแยกออกจากธาตุอื่นๆ ทำให้มีความแข็งที่ไม่สม่ำเสมอ บางจุดจะมีความแข็งต่ำ ซึ่งมีผลต่อการสึกหรอของคมตัดเป็นอย่างมากเมื่อนำไปใช้งาน
- วัสดุ HSS จะมีความแข็งลดต่ำลงเป็นอย่างมาก ถ้าอุณหภูมิมากกว่า 400 °C จึงทำให้วัสดุ HSS ต้องใช้ความเร็วตัดต่ำกว่าคาร์ไบด์หรือเซรามิคมาก
ถึงแม้ว่าจะมีการนำคาร์ไบด์มาใช้งานกันมากขึ้น แต่วัสดุ HSS ก็ยังคงมีการใช้งานกันอยู่มากในงานประเภท ดอกสว่าน รีมเมอร์ ดอกต๊าป เครื่องมือทำเกลียว เอ็นมิล และมีดกัดเฟือง ในกลุ่มงานเครื่องมือที่ซับซ้อนพวกเครื่องมือขึ้นรูป เครื่องมือตัดที่ต้องการขอบคมตัดหรือมุมที่มีความคม เช่น Broaches ก็ยังคงใช้วัสดุ HSS เป็นวัสดุคมตัด
วัสดุ HSS จะใช้งานกันมากในการทำงานที่มีความเร็วตัดต่ำกับเครื่องจักรที่มีกำลังต่ำ และไม่แข็งแรงสำหรับงานหนัก อีกเหตุผลที่ใช้วัสดุ HSS คือการที่มีต้นทุนการผลิต ผลิตได้ง่าย มีความเหนียว เป็นวัสดุอเนกประสงค์ในงานตัดเฉือนทั่วไป
วัสดุ HSS โคบอลท์ ( HSS Cobalt ) เป็นเกรดที่เติมโคบอลท์เพิ่มเติมเข้าไป นิยมนำมาใช้งานมากขึ้น เนื่องจากทนต่อการสึกหรอได้ดีขึ้น มีความแข็งสูง ทนต่อความร้อนได้มากขึ้น ตามสัดส่วนของโคบอลท์ที่ผสมเพิ่มเข้าไป ทำให้อายุการใช้งานนานกว่า HSS เกรดทั่วไปที่ไม่มีโคบอลท์เป็นส่วนผสม
2. เหล็กรอบสูงประเภทผงโลหะ HSS-PM ( Powdered Metal High-Speed Tool Steel, HSS-PM )
เหล็ก HSS-PM จะมีโครงสร้างเกรนของธาตุเจือและคาร์ไบด์ ที่มีความละเอียดและสม่ำเสมอ ไม่เกิดการแยกตัวขึ้นในโครงสร้าง ช่วยให้กระบวนการผลิตสามารถใช้วัสดุที่มีสมบัติดีขึ้นและมีส่วนผสมของอัลลอยในสัดส่วนที่สูงขึ้น ทำให้ HSS-PM มีความแข็งและความเหนียวที่สูงกว่าวัสดุ HSS เกรดพื้นฐาน จึงนิยมนำมาใช้งานกันแพร่หลายมากขึ้น
ถึงแม้ว่าในกระบวนการผลิตวัสดุ HSS-PM จะมีต้นทุนที่สูงกว่าวัสดุ HSS เกรดพื้นฐาน แต่วิธีการผลิตและประสิทธิภาพการใช้งานที่ได้จากวัสดุที่ผลิตด้วยผงโลหะ สามารถจะชดเชยต้นทุนที่เพิ่มสูงขึ้นได้เป็นอย่างมาก
ข้อดีที่สำคัญของวัสดุ HSS-PM คือ กระบวนการผลิตจากผงโลหะ ทำให้การออกแบบมีความยืดหยุ่นสูงขึ้น สามารถสร้างเครื่องมือที่มีรูปร่างที่ซับซ้อน เช่นมีรูน้ำหล่อเย็นที่เป็นมุมเลื้อยตามร่องคมตัดได้ ซึ่งถ้าไปผลิตด้วยกระบวนการผลิตวัสดุ HSS จากการหล่อและตีขึ้นรูปจะไม่สามารถทำได้หรือมีต้นทุนการผลิตที่สูงกว่า
การนำไปใช้งาน (Application)
วัสดุ HSS-PM นำไปใช้กับมีดกัดเป็นส่วนใหญ่ อัตราการกัดโลหะโดยทั่วไปจะสูงกว่าวัสดุ HSS พื้นฐาน ด้วยวัสดุ HSS-PM สามารถใช้ความเร็วตัดและอัตราป้อนที่สูงขึ้น ซึ่งโดยทั่วไปจะเพิ่มอัตราการกัดต่อฟันในการกัดหยาบหรือเพิ่มความเร็วตัดในการเก็บละเอียด
ชนิดของวัสดุ HSS ในงานวัสดุงานตัดเฉือนโลหะ
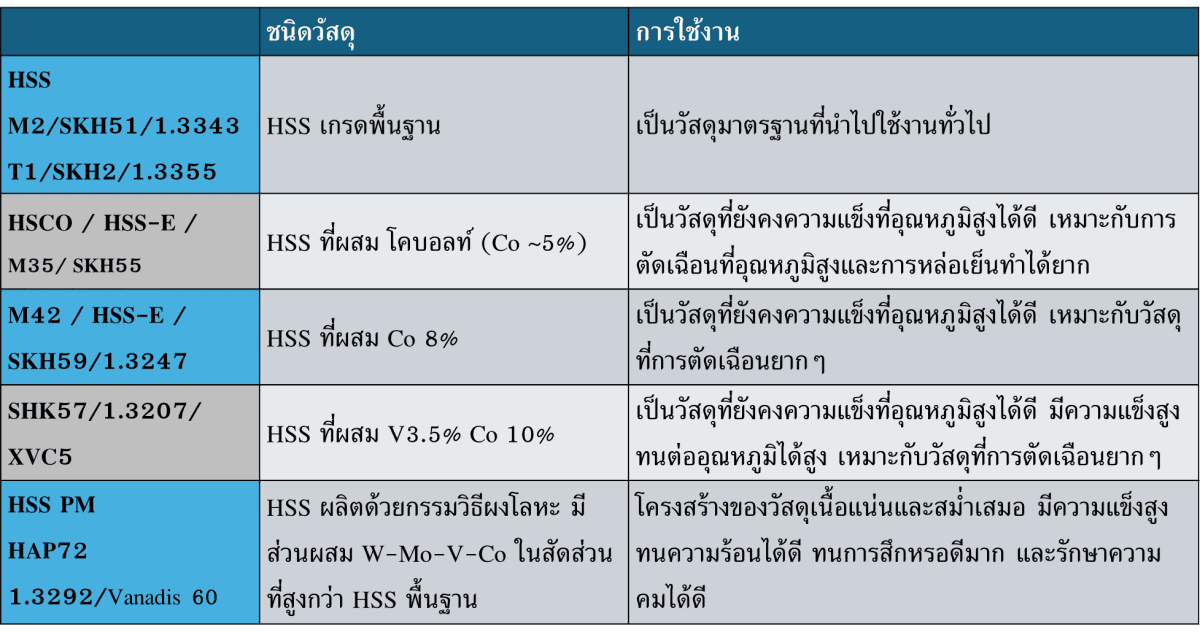
3. วัสดุหล่ออัลลอยโคบอลต์ (Cobalt-Based Alloy)
วัสดุอัลลอยผสมโคบอลท์ – โครเมี่ยมและทังสเตน วัสดุประเภทนี้ผลิตขึ้นมาเฉพาะตามผู้ผลิตแต่ละราย โดยโลหะหลอมเหลวจะถูกหล่อในแม่พิมพ์ที่เย็นซึ่งทำจากวัสดุกราไฟท์ ด้วยการเย็นตัวที่รวดเร็วในแม่พิมพ์ จะทำให้ได้โครงสร้างเป็นเกรนละเอียด ผิวมีความแข็งสูงและภายในเนื้อวัสดุมีความเหนียวที่ดี
มีดตัดที่หล่อจากอัลลอยโคบอลท์ จะเป็นเครื่องมือตัดที่มีสมบัติระหว่างกลางของวัสดุ HSS กับมีดตัดคาร์ไบด์ ที่การทำงานในลักษณะความเร็วตัดสูงไปกับวัสดุ HSS แต่จะช้าไปถ้าใช้กับมีดตัดคาร์ไบด์
มีดตัดที่ผลิตจากวัสดุหล่อประเภทนี้ จะเหมาะสมเป็นอย่างยิ่งกับเครื่องมือหรือการทำงานที่มีการใช้เป็นมีดตัดหลายๆ ชนิดประกอบเข้าด้วยกัน ซึ่งเครื่องจักรมีข้อจำกัดในเรื่องการใช้ความเร็วรอบ มีดตัดวัสดุหล่ออัลลอยโคบอลท์ทนต่อการแตกหักได้ดีกว่าวัสดุคาร์ไบด์ และทนต่อความร้อนได้สูงกว่าวัสดุ HSS ด้วยความแข็งแรงที่สามารถทนต่อการแตกหักได้ดี การตัดเฉือนแบบไม่ต่อเนื่องและมีการกระแทกดีกว่าวัสดุคาร์ไบด์ มีความแข็งแรงที่สูง และสัมประสิทธิแรงเสียดทานต่ำ จึงเหมาะที่จะนำไปใช้งานที่ใช้ความเร็วต่ำและแรงดันสูงๆ เช่นพวกการตัดขาดหรือการทำร่องได้ดี
4. ซีเมนต์คาร์ไบด์ (Cemented Carbide)
วัสดุซีเมนท์ทังสเตนคาร์ไบด์มีโครงสร้างคล้ายกับซีเมนท์ เปรียบเสมือนว่าตัวคาร์ไบด์เป็นก้อนกรวดและวัสดุโคบอลท์เปรียบเหมือนปูนซีเมนท์ทำหน้าที่เป็นตัวประสานวัสดุต่างๆ เข้าด้วยกัน เกรนของทังสเตนคาร์ไบด์จะหลอมเข้าในเนื้อของเมตริกโลหะโคบอลท์ด้วยกระบวนการซินเตอร์ ( Sintering ) ที่อัดขึ้นรูปของธาตุต่างๆ โดยอยู่ในรูปผงโลหะด้วยแรงดันสูง ต่อด้วยกระบวนการให้ความร้อนที่อุณหภูมิสูง ทำให้ได้วัสดุที่มีความแข็งสูงและประสานเข้าด้วยกัน คาร์ไบด์เป็นวัสดุที่มีความแข็งสูงเหมาะกับกระบวนการตัดเฉือนในปัจจุบันและมีการใช้งานกันแพร่หลาย
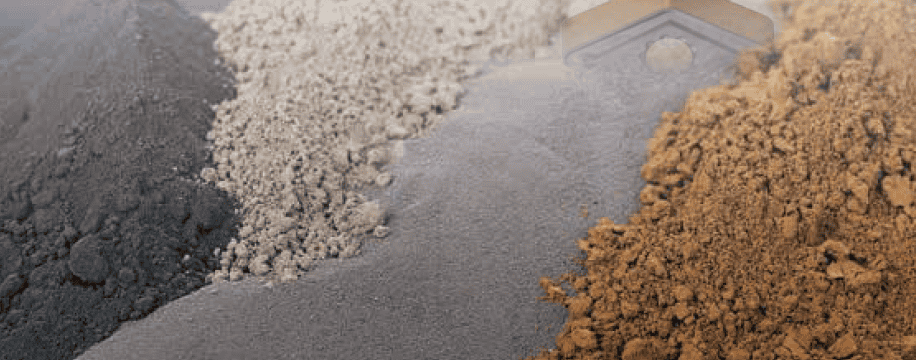
ทังสเตนคาร์ไบด์ ( Tungsten Carbide WC ) เป็นวัสดุคอมโพสิทที่ผลิตด้วยกระบวนการผงโลหะ ( Powder Metallurgy ) สัดส่วนของผงทังสเตนคาร์ไบด์โดยทั่วไปจะมีสัดส่วนประมาณ 70-97% โดยน้ำหนัก และนำมาผสมเข้ากับวัสดุประสาน ซึ่งปกติจะเป็นโคบอลท์นำวัสดุทั้งหมดมาอัดในแม่แบบ ( Die ) แล้วไปผ่านกระบวนการซินเตอร์ในเตาที่ความร้อนสูงกว่า 1200°C ซีเมนต์คาร์ไบด์อาจจะเป็นส่วนผสมของไททาเนียมคาร์ไบด์ ( Titanium Carbide ( TiC )) เทนทาลัม ( Tantalum Carbide ( TaC )) ไนโอเบียม ( Niobium Carbide ( NbC )), แคลเซี่ยม ( Calcium Carbide ), ซิลิกอนคาร์ไบด์ ( Silicon Carbide ), อลูมิเนียม ( Aluminum Carbide ) ไอร์อน( Iron Carbide )
ข้อดีของซีเมนท์คาร์ไบด์คือมีความแข็งที่สูงมากทั้งที่อุณหภูมิห้องและที่อุณหภูมิสูง ทำให้เหมาะที่จะนำมาใช้ทำวัสดุในงานตัดเฉือนโลหะ คาร์ไบด์เกรดที่มีความแข็งต่ำสุดก็ยังแข็งสูงกว่าวัสดุเหล็ก HSS ที่มีความแข็งมากที่สุด
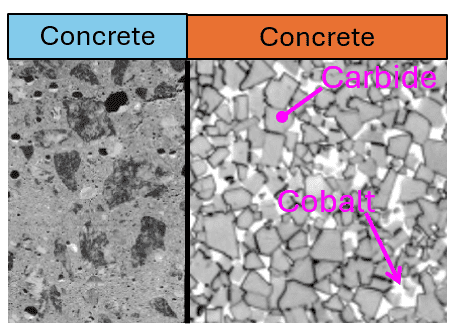
คาร์ไบด์จะมีขนาดของเกรนที่ไม่เท่ากัน ซึ่งจะเหมาะกับการตัดเฉือนหรือประเภทการใช้งานที่แตกต่างกันไป คาร์ไบด์เกรนที่นิยมนำมาใช้ในการทำเอนมิลล์ได้แก่เกรด Micro-Grain และ Submicron ขนาดของเกรนที่ต่ำกว่า 1μm จะมีความแข็งสูงที่สูง ทนต่อการสึกหรอและทนต่อการแตกหักได้ดี
Rough | ≥ 1.3 |
Micro Grain | 0.8 ≤ 1.3 |
Submicron | 0.5 ≤ 0.8 |
Ultrafine | 0.2 ≤ 0.5 |
Nano | < 0.2 |
ตารางแสดงขนาดของเม็ดเกรนคาร์ไบด์
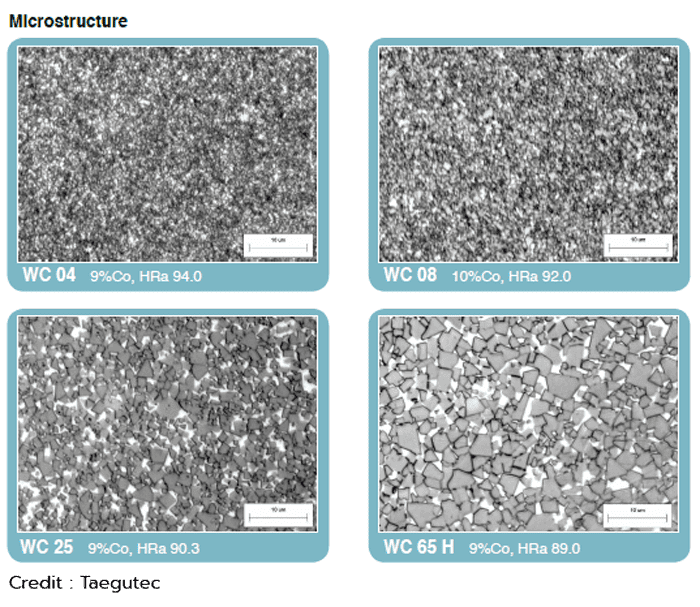
5. เซอร์เมท (Cermet)
เซอร์เมท (Cermet) หรือเซรามิคคอมโพสิท เป็นวัสดุผสมระหว่างเซรามิคกับโลหะ (Ceramic + Metal) โดยใช้ไททาเนียมคาร์ไบด์เป็นอัลลอยผสม แทนที่จะเป็นทังสเตนคาร์ไบด์ วัสดุมีดตัดประเภทนี้เป็นวัสดุที่อัดขึ้นรูปร้อนโดยทั่วไปมีสีดำ
เซอร์เมทเป็นวัสดุที่มีความแข็งสูงกว่าคาร์ไบด์ ทนต่อความร้อน ปฏิกิริยาเคมีออกซิเดชั่นได้ดี อีกทั้งยังช่วยลดการเกาะติดของเศษวัสดุและผิวมีความเสียดทานที่ต่ำกว่าคาร์ไบด์ จึงเหมาะกับงานที่ต้องการความเร็วตัดที่สูงกว่าคาร์ไบด์ ค่าความหยาบผิวที่ดีขึ้น ทนต่อการเสียหายจากความร้อนได้ดีกว่าวัสดุคาร์ไบด์ แต่จะด้อยกว่าคาร์ไบด์ในเรื่องการทนต่อแรงกดและการทนต่อการเปลี่ยนอุณหภูมิแบบฉับพลัน (Thermal Shock) ได้ต่ำลง เซอร์เมทจะเหมาะกับการใช้งานพวกวัสดุอ่อนที่เกิดการพอกของเศษที่หน้าคมตัด งานเก็บละเอียดที่ต้องการพิกัดขนาดแคบๆ ที่ต้องการอายุการใช้งานของมีดตัดนานขึ้นและให้ผิวงานที่เรียบขึ้น สามารถใช้งานได้ดีกับสเตนเลส เหล็กหล่อเหนียว ( Ductile Cast Iron) เหล็กคาร์บอนต่ำและวัสดุกลุ่มเหล็กทั่วไป
6. เซรามิก (Ceramic)
เซรามิคเราอาจจะคุ้นเคยกับวัสดุในกลุ่มนี้ในอีกชื่อว่าอลูมินั่มออกไซด์ เป็นวัสดุที่ทนต่อความร้อน มีความแข็งและทนต่อการสึกหรอได้ดี แต่มีข้อด้อยคือไม่ชอบการเปลี่ยนแปลงอุณหภูมิแบบฉับพลันที่รุนแรง เป็นวัสดุที่แตกร้าวได้ง่ายเมื่อเกิดแรงกระทำ ยุคแรกที่พัฒนาขึ้นในงานตัดเฉือนวัสดุยังใช้งานได้ไม่ดี ทั้งในแง่สมบัติของวัสดุเองและการนำไปใช้งาน ต่อมาได้ปรับปรุงพัฒนาในหลายๆ ด้าน โดยการทำให้ขนาดเกรนละเอียดขึ้น และการควบคุมความหนาแน่น การปรับปรุงการผลิตสารเติมแต่งให้มีสมบัติที่ดีขึ้น การเจียเม็ดมีดได้พัฒนาให้ดีขึ้น และการปรับขอบคมตัดให้เหมาะสมต่อการใช้งาน ทำให้มีดตัดวัสดุ
ข้อดีของวัสดุตัดเซรามิค
- การเพิ่มผลิตภาพในการใช้งานหลายประเภท มีดตัดเซรามิคสามารถทำงานที่ความเร็วตัดสูงกว่ามีดตัดทังสเตนคาร์ไบด์ การใช้งานโดยส่วนใหญ่จะมีอัตราการกัดเนื้องานที่สูง ด้วยคุณสมบัติของเซรามิคที่ดีเช่นการรักษาความแข็งได้ดีที่อุณหภูมิสูงๆ สัมประสิทธิ์แรงเสียดทานต่ำ ทนต่อการสึกหรอได้สูงทนต่อปฏิกิริยาเคมี
- มีสัมประสิทธิ์การถ่ายเทความร้อนต่ำ ซึ่งทำให้ความร้อนเกือบทั้งหมดที่เกิดจากการตัดเฉือนจะออกไปกับเศษตัด ทำให้ความร้อนที่เกิดขึ้นกับชิ้นงาน เม็ดมีดและตัวจับยึดเครื่องมือตัดมีอุณหภูมิที่ต่ำกว่ามีดคาร์ไบด์
- คุณภาพของชิ้นงานสูงขึ้น การควบคุมขนาดทำได้ดีขึ้น อันเนื่องมาจากการสึกหรอของมีดตัดน้อยลง และยังคงรักษาผิวสำเร็จของชิ้นงานจากการตัดเฉือนได้นานขึ้น ควบคุมขนาดได้ดี
- มีดตัดเซรามิคยังนำไปใช้ในการตัดเฉือนโลหะที่มีความแข็งสูงๆ ได้หลายประเภท และบ่อยครั้งที่สามารถนำไปทดแทนขั้นตอนการเจียระไนได้
ข้อจำกัดของวัสดุตัดเซรามิค
- การใช้งานต้องใช้ด้วยความระมัดระวังเป็นพิเศษ เพราะมีดตัดวัสดุเซรามิตจะมีความเปราะมากกว่าคาร์ไบด์ การเกิดแรงกระแทกจะต้องต่ำหรือน้อยที่สุด รวมทั้งการเกิดความร้อนแบบฉับพลันก็เป็นประเด็นที่ต้องหลีกเลี่ยง
- มีดตัดเซรามิคสามารถนำไปใช้กับงานที่มีการตัดเฉือนแบบไม่ต่อเนื่อง แบบเบาๆ ถึงปานกลางได้บ้าง แต่ไม่แนะนำเป็นอย่างยิ่งในการนำไปใช้กับงานที่มีการตัดเฉือนแบบไม่ต่อเนื่องหนักๆ
7. CBN (Cubic Boron Nitride Tool)
CBN เป็นวัสดุมีดตัดที่มีความแข็งเป็นอันดับสองรองจากเพชร รักษาความแข็งได้ดีที่อุณหภูมิสูง จึงสามารถใช้งานความเร็วตัดสูงๆ ได้ดี อีกทั้งยังเป็นวัสดุที่มีความเหนียว และทนต่อการเปลี่ยนอุณหภูมิแบบฉับพลันได้ดี
เกรดวัสดุ CBN รุ่นใหม่ๆ จะมีเซรามิคเป็นส่วนผสมอยู่ วัสดุหลักจะมี CBN ผสมอยู่ประมาณ 40 – 65% ส่วนผสมเซรามิคที่เป็นวัสดุประสานจะช่วยเพิ่มความทนต่อการสึกหรอให้กับ CBN และทนต่อปฏิกิริยาทางเคมีได้ดีขึ้น ส่วนวัสดุ CBN อีกกลุ่มจะมีส่วนผสม CBN อยู่ประมาณ 85 – 100% และส่วนที่เหลือเป็นโลหะเป็นวัสดุประสาน CBN กลุ่มนี้จะมีความเหนียวสูงขึ้นกว่ากลุ่มแรก
การนำไปใช้งานวัสดุ CBN จะถูกบัดกรีเข้ากับเม็ดอินเสิร์ทคาร์ไบด์ นิยมนำไปใช้งานกลึงผิวสำเร็จทดแทนกระบวนการเจียระไนกับเหล็กชุบแข็งที่มีความแข็งสูงกว่า 45 HRC ไม่แนะนำไปใช้กับเหล็กที่มีความแข็งต่ำกว่า 45 HRC จะทำให้เกิดการสึกหรอของวัสดุ CBN ในการตัดเฉือนอย่างมาก
CBN สามารถนำมาใช้ในการกัดหยาบที่ความเร็วตัดสูงๆ กับวัสดุเหล็กหล่อสีเทา ใช้งานได้ทั้งงานกัดและงานกลึง

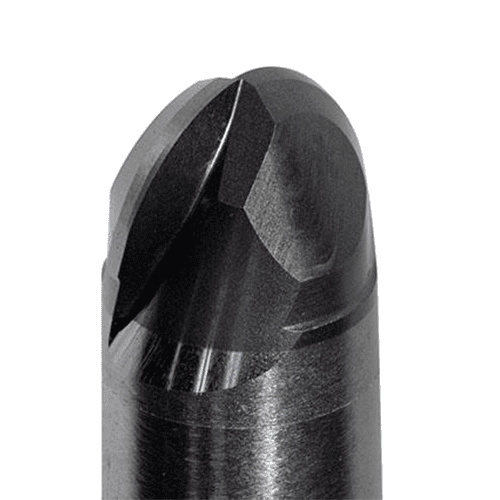
8. เพชร (Diamond)
เพชร PCD เป็นวัสดุคอมโพสิตที่ขึ้นรูปด้วยกระบวนการซิลเตอร์เข้ากับโลหะที่ทำหน้าที่เป็นตัวประสาน PCD จะมีความแข็งต่ำกว่า MCD แต่ก็ยังมีความแข็ง และทนต่อการสึกหรอได้ดีกว่าวัสดุประเภทอื่น PCD จะมีข้อเสียที่ไม่เสถียรทางเคมีที่อุณหภูมิสูง และละลายตัวในเหล็กได้เช่นเดียวกับเพชร MCD
การใช้งาน PCD จะใช้งานกับวัสดุนอกกลุ่มเหล็กและอโลหะเท่านั้น เช่น High-Silicon Aluminium, Metal Matrix Composites (MMC) และพลาสติกเสริมใยคาร์บอนไฟเบอร์ (Carbon Fiber-Reinforced Plastic (CFRP)) เป็นต้น การนำ PCD ไปใช้งานตัดเฉือนร่วมกับการฉีดน้ำหล่อเย็น สามารถนำมาใช้งานเก็บผิวละเอียดมาก ๆ กับวัสดุไทเทเนียม (Superfinishing Application) ได้ดี
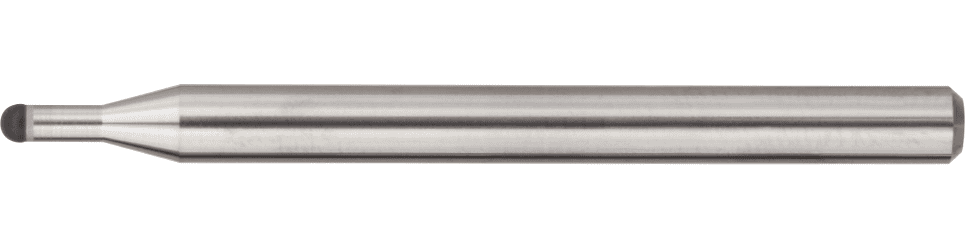