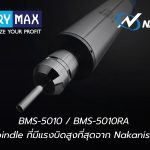
Nakanishi Motor Spindle รุ่นใหม่ที่พัฒนาให้มีแรงบิดสูงขึ้น
September 20, 2024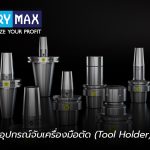
อุปกรณ์จับเครื่องมือตัด Tool Holder
October 1, 2024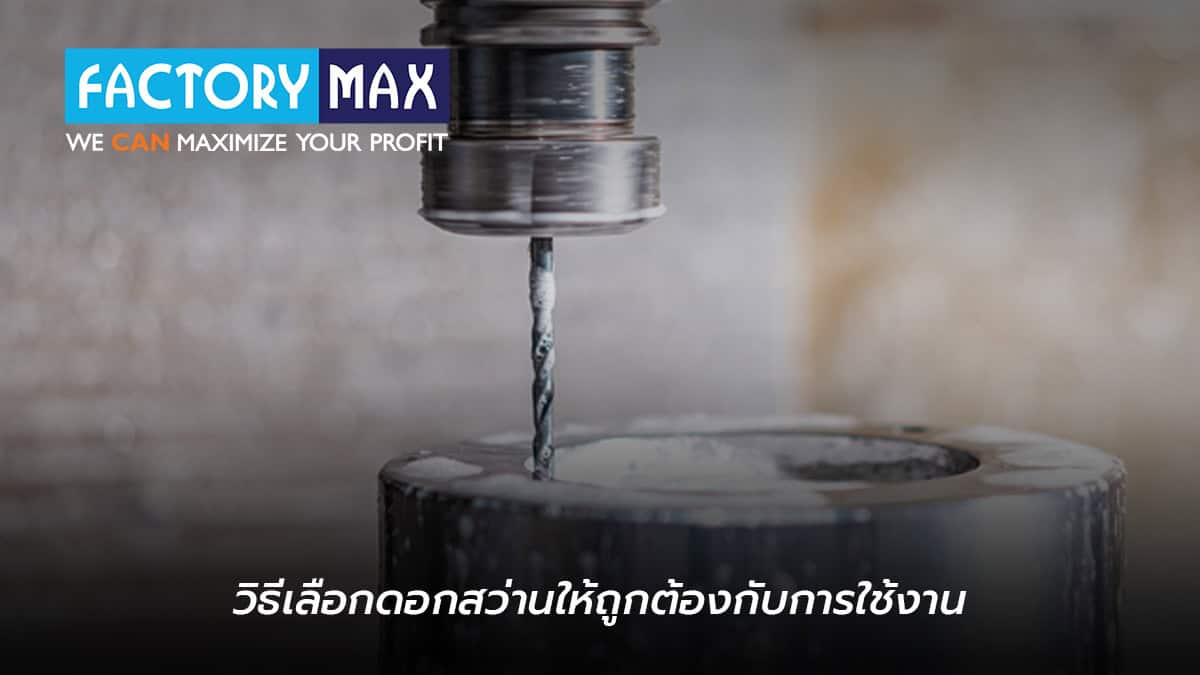
เลือกอ่านประเด็นที่สนใจ
- ดอกสว่านเจาะรูลึก
- ดอกสว่านเจาะรูขนาดเล็ก
- การเจาะรูทะลุถึงกัน (Cross Hole Processing)
- ปัญหาและแนวทางการแก้ไขในงานเจาะ
- สิ่งที่คุณจำเป็นต้องรู้เกี่ยวกับดอกสว่าน
การเลือกดอกสว่านตามชนิดของวัสดุดอกสว่าน
วัสดุดอกสว่านจะมีวัสดุหลายประเภท HSS, คาร์ไบด์, เซอร์เม็ท, เซรามิค, CBN และเพชร แต่โดยทั่วไปส่วนใหญ่จะเป็นวัสดุ HSS หรือ คาร์ไบด์ ซึ่งมีการใช้งานแพร่หลายมากกว่า
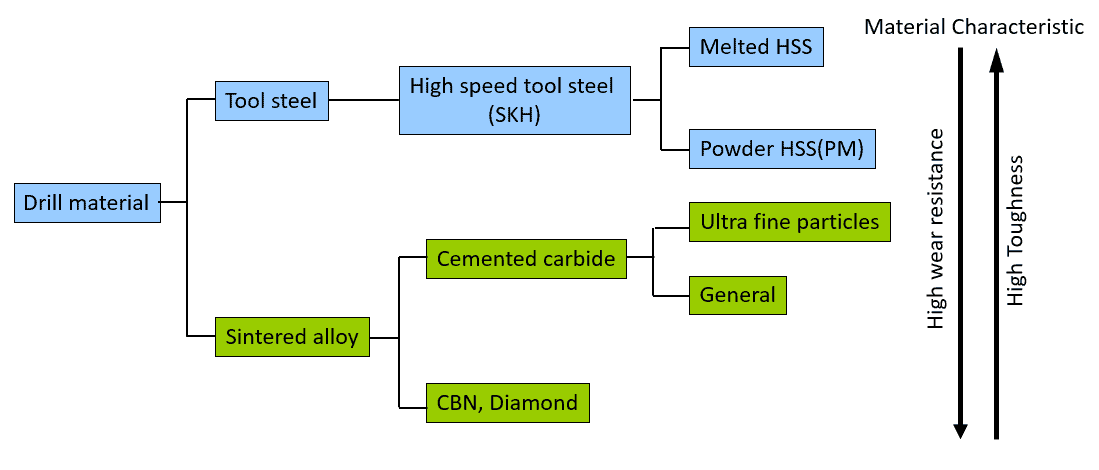
ตารางวัสดุดอกสว่านและเกณฑ์ในการเลือกใช้
สภาวะการทำงาน | เกณฑ์ | วัสดุดอกสว่าน | |
HSS | คาร์ไบด์ | ||
ความแข็งแรงของอุปกรณ์ *รวมทั้งหัวจับสว่าน | ดี | 〇 | 〇 |
ต่ำ | △ | X | |
การหนีศูนย์ของหัวจับสว่าน (Drill holder runout) | มาก | △ | X |
น้อย | 〇 | 〇 | |
ความแข็งของวัสดุงาน (มากกว่า 40 HRC) | ความแข็งสูง | X | 〇 |
ความแข็งต่ำ | 〇 | 〇 | |
ความเร็วตัด (มากกว่า 50 m / min) * ใช้กับเหล็กคาร์บอน | ความเร็วตัดสูง | X | 〇 |
ความเร็วตัดต่ำ | 〇 | 〇 |
ระยะของร่องคายเศษ (Groove Length)
ความยาวของร่องคายเศษน้อยสุด จะกำหนดจากวิธีการคำนวณดังต่อไปนี้
DC = ขนาดเส้นผ่านศูนย์กลางของดอกสว่าน
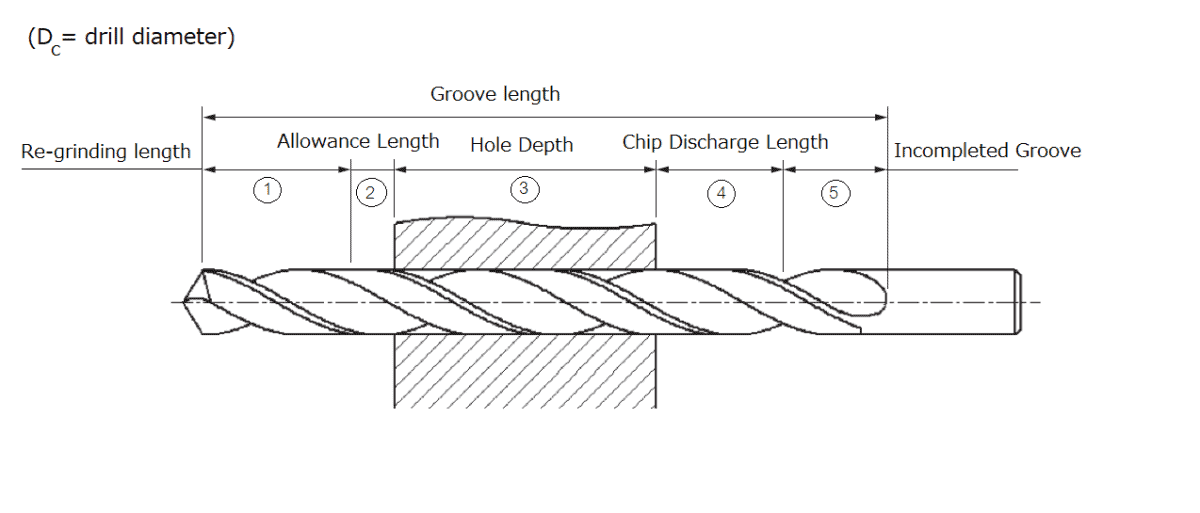
Groove length = ③ Machining Hole Depth + Chip Discharge Allowance ((④ Chip Discharge Length (α x DC) + ⑤ Incompleted Groove 1 x DC) + ① Re-Grinding Length + ② Allowance Length (β x DC)
ความยาวของร่อยคายเศษ = ③ ความลึกของรูเจาะ + ความยาวของการคายเศษทั้งหมด ( ④ ระยะคายเศษ (α x DC) + ⑤ ระยะปลายร่องเลื้อย (1 x DC)) + ① ระยะลับคมใหม่ + ② ระยะเผื่อเจาะ (β x DC))
ตารางค่าสัมประสิทธิระยะเผื่อการคายเศษของดอกสว่าน (α)
วัสดุชิ้นงาน | α |
อะลูมิเนียม | 1.5-2 |
สเตนเลส | 1.5-2 |
เหล็ก | 1.0-1.5 |
เหล็กหล่อ | 0-0.5 |
ตารางค่าสัมประสิทธิระยะเผื่อเจาะ (β)
ประเภทของรูเจาะ | β |
รูตัน | 0 |
รูทะลุ | มากกว่า 1 |
ความยาวของร่องเลื้อยคายเศษ เป็นระยะจากปลายคมตัดสว่านถึงส่วนปลายของร่องคายเศษ แต่ในบริเวณส่วนปลายของร่องคายเศษ ค่าความลึกจะค่อย ๆ ตื้นขึ้น ความยาวของร่องทั้งหมดจะเป็นผลรวมของส่วนปลายร่อง ระยะเผื่อการคายเศษ และค่าความลึกของรูเจาะ ในทางปฏิบัติความยาวของร่องคายเศษควรจะเผื่อระยะการนำไปลับคมตัดใหม่ด้วย
*** หมายเหตุ สว่านที่มีความยาวมากกว่าดูเหมือนจะประหยัดกว่าสว่านที่สั้น เพราะสามารถนำกลับไปลับคมใหม่ได้มากกว่า แต่ตัวสว่านจะอ่อนแอกว่า และในขณะเจาะงานจะเกิดการสั่นมากขึ้น ทำให้ลดความเที่ยงตรงของรูเจาะและทำให้ดอกสว่านเกิดการสึกหรอเร็วกว่าปกติ ส่งผลต่ออายุการใช้งานของดอกสว่านที่สั้นลง
สว่านประเภทพิเศษ
ดอกสว่านเจาะรูลึก
ในการเจาะรูที่มีความลึกมาก ๆ เศษจะอยู่ในรูเจาะนานขึ้น และน้ำมันตัดเฉือนจะไม่สามารถแทรกเข้าสู่บริเวณคมตัดได้ดีพอ ส่งผลให้เกิดแรงต้านการเจาะเพิ่มสูงขึ้น ทำให้การควบคุมความเสถียรของงานเจาะทำได้ยาก
โดยปกติในการเจาะรูโดยทั่วไป ความลึกของรูเจาะจะประมาณ 3 เท่าของเส้นผ่านศูนย์กลาง (หรือ 3D-4D, D = เส้นผ่านศูนย์กลางของรูเจาะ) ในการเจาะรูเมื่อความลึกมากขึ้น เศษเจาะจะเริ่มไหลได้ยากและมีโอกาสเกิดการอุดตันได้มากขึ้น จำเป็นที่จะต้องยกดอกสว่านในขณะเจาะเพื่อคลายเศษออกสู่ภายนอก
รูปดอกสว่าน HSS ที่คายเศษได้ง่ายและมีความแข็งแรงสูง สำหรับเจาะรูที่มีความลึกมาก ๆ ถึง 50 เท่าของเส้นผ่านศูนย์กลางดอกสว่าน (50D)
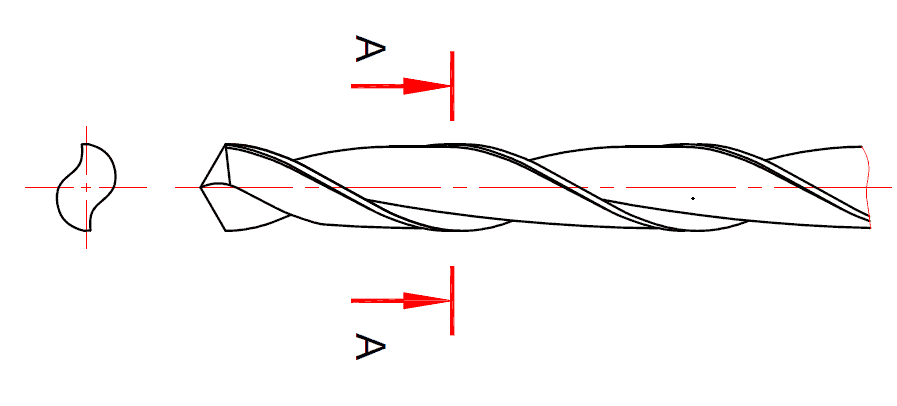

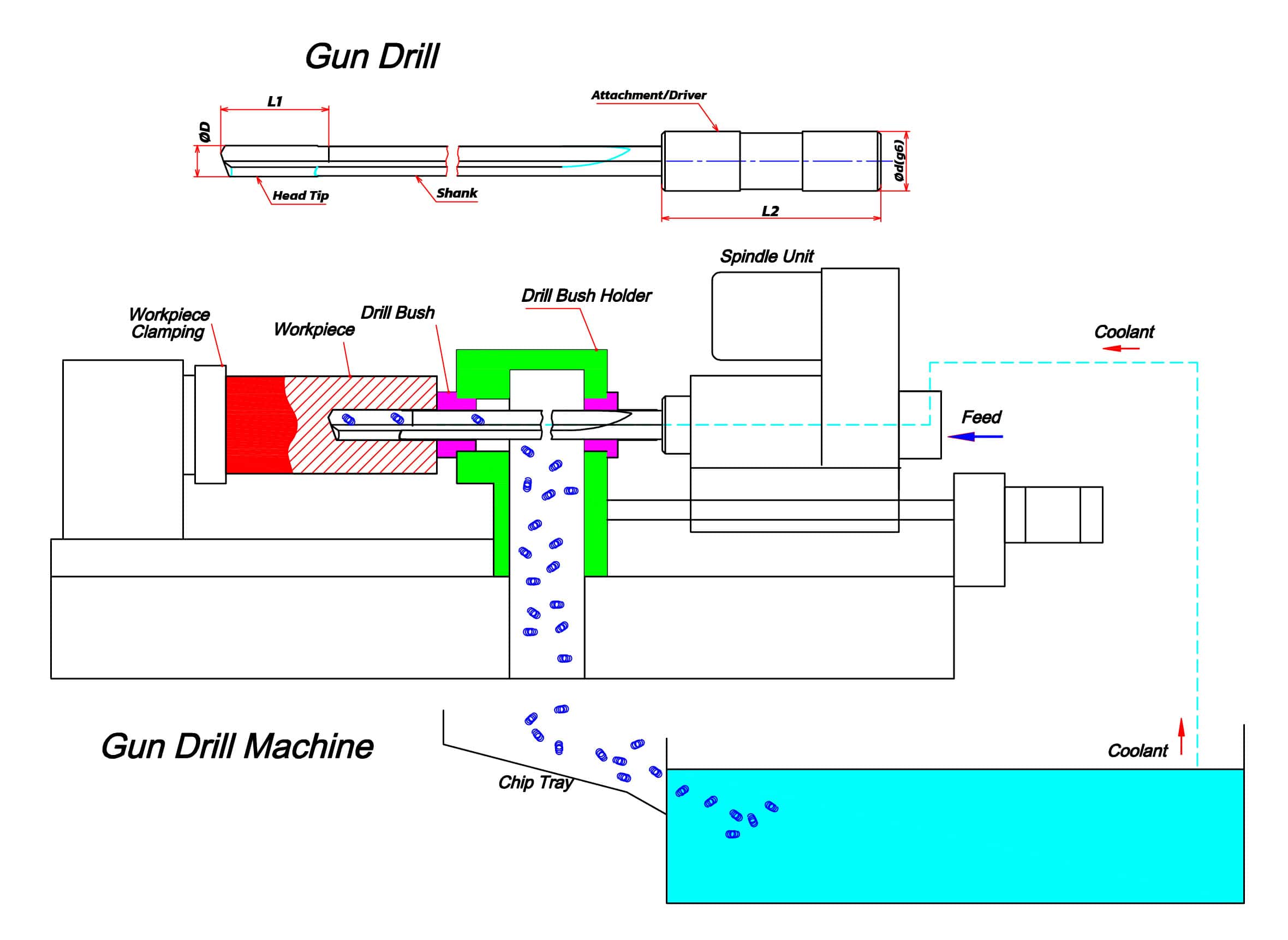
ดอกสว่านเจาะรูขนาดเล็ก
ถึงแม้ยังไม่มีข้อกำหนดเรื่องสว่านในการเจาะรูขนาดเล็กว่ามีขนาดเป็นเท่าใด โดยทั่วไปจะหมายถึงการเจาะรูที่มีขนาดเล็กกว่า 3 มิลลิเมตร ถ้าเปรียบเทียบกับดอกสว่านคาร์ไบด์ ดอกสว่าน HSS จะมีการแตกหักที่น้อยกว่า และนิยมนำมาใช้กับงานที่มีความละเอียดสูง งานหัวฉีด (หัวฉีดเชื้อเพลิงในงานยานยนต์ หัวฉีดใยเคมี) และงานนาฬิกา ส่วนดอกสว่านคาร์ไบด์ในปัจจุบันจะใช้กันอย่างมากในการเจาะรูเล็ก ๆ พวกงานแผ่นวงจรไฟฟ้า (Print Circuit Board) ด้วยคุณภาพของคาร์ไบด์เกรนละเอียดพิเศษ (Ultra fine Grain Cemented Carbide) สามารถทนต่อการแตกหักได้ดีมาก จึงนำมาใช้งานเจาะเหล็กและสเตนเลสได้ดีเช่นกัน
นอกจากนี้ในงานเจาะรูลึก ๆ และละเอียด ที่มีขนาดเล็กกว่า 1mm การเจาะรูวิธีการ EDM ก็นิยมใช้กันมาก แต่ปัจจุบันนี้ดอกสว่านคาร์ไบด์เคลือบผิวที่มีขนาด 0.04-1mm ความยาวช่วงคอร์ (Neck Length) 10D -50D ก็ได้พัฒนาขึ้นมาก และสามารถนำมาใช้งานเจาะรูลึกที่ละเอียดได้ดี ดังรูปภาพ
การเจาะรูทะลุถึงกัน (Cross Hole Processing)
การเจาะรูแบบทะลุถึงกัน คือรูเจาะจะมีจำนวนมากกว่า 2 รูเจาะทะลุถึงกันที่มุมต่าง ๆ การเจาะรูในลักษณะนี้เป็นสาเหตุที่ทำให้รูเจาะเกิดการเลื้อย หรือเกิดการสึกหรอของสันคมเลื้อย จากการสั่นหรือการดิ้นของดอกสว่าน อาจส่งผลทำให้เกิดการแตกหักของดอกสว่าน จากสาเหตุของเศษเจาะและครีบที่เกิดขึ้น นอกจากนี้แล้วยังทำให้อายุการใช้งานของดอกสว่านสั้นลงด้วย เพื่อให้ได้คุณภาพของรูเจาะที่ดี และหลีกเลี่ยงการเสียหายของดอกสว่าน แนะนำให้ใช้ดอกสว่านแบบ Double Margin เพื่อให้แน่ใจว่าดอกสว่านสามารถรักษาศูนย์รูเจาะได้ดี และลดการสั่นหรือดิ้นของดอกสว่าน ขณะเจาะผ่านรูเจาะที่ทะลุถึงกัน
การลบสันมุมจิกที่ปลายดอกสว่าน และการลดอัตราป้อนลงครึ่งหนึ่งในขณะกำลังเจาะรูทะลุถึงกัน จะช่วยลดปัญหาลงได้เป็นอย่างมาก
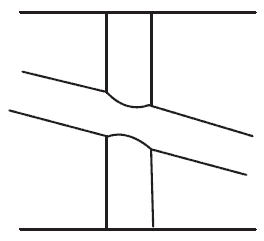
ปัจจุบันด้วยการปรับปรุงรูปทรงของปลายดอกสว่าน ร่องคมเลื้อย และการพัฒนาเรื่องการควบคุมเศษเจาะ มุมจิก 180° ได้ถูกนำมาใช้กันมากขึ้น ทำให้การเจาะมีประสิทธิภาพที่ดีขึ้น ทั้งในงานเจาะรูที่มีความหนาไม่สม่ำเสมอ เช่น Cross-Hole, Counterbore และรูที่ผ่านกระบวนการหล่อมาก่อนหน้า
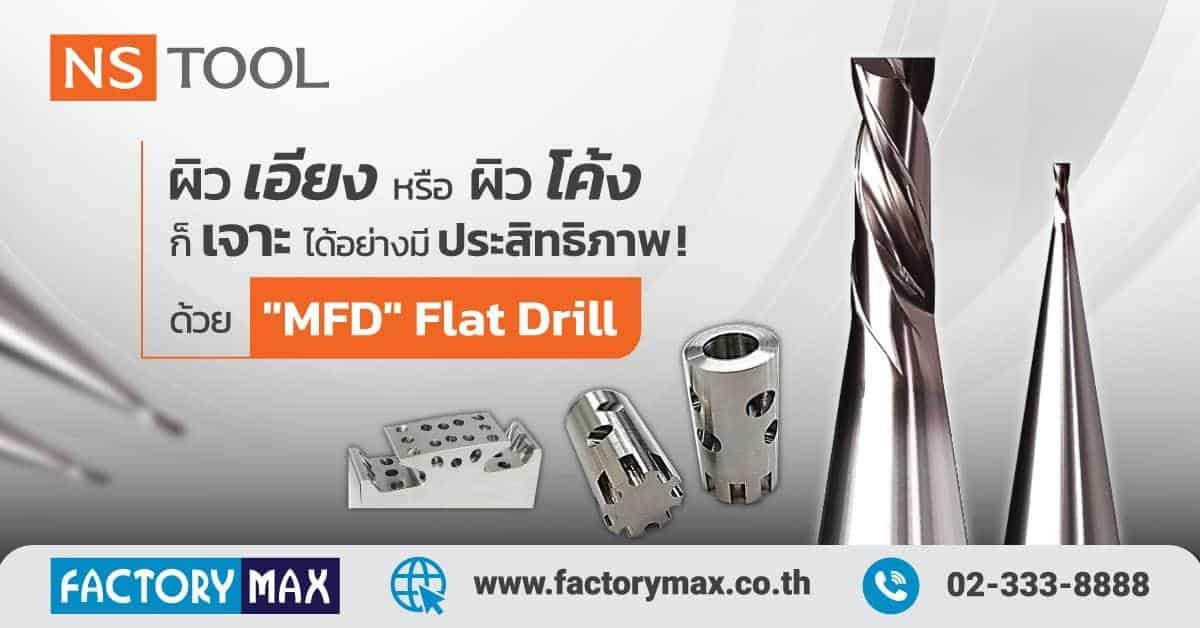
ปัญหาและแนวทางการแก้ไขในงานเจาะ
ปัญหาของรูเจาะไม่เพียงแค่ที่เกิดขึ้นกับคมตัดของดอกสว่านเท่านั้น แต่รวมทั้งความผิดพลาดของรูเจาะที่ได้ ความคลาดเคลื่อน ค่าเบี่ยงเบนจากมาตรฐาน เศษตัดเกิดการห่อตัวหรืออุดตันขึ้น การเกิดครีบ หรือการแตกหักของดอกสว่าน
ปัญหาที่เกิดขึ้นในงานเจาะและแนวทางการแก้ไข
ปัญหาที่เกิดขึ้น | สาเหตุ | การแก้ไข |
ขนาดรูเจาะโต | 1. จับดอกสว่านได้ไม่ร่วมศูนย์ 2. เพลาขับของเครื่องหนีศูนย์มากเกินไป 3. มุมของดอกสว่านไม่สมมาตร 4. ความสูงของคมตัดแตกต่างกันมากไป 5. ความไม่สมมาตรของคมจิกดอกสว่าน | 1. ตรวจสอบความเรียบร้อยของหัวจับ ปลอก Sleeves 2. ตรวจสอบการหมุนของเพลา 3. ลับคมตัดให้ถูกต้อง |
ขนาดของรูเจาะมีค่าแตกต่างกันมาก | 1. การสึกหรอของสันคมเลื้อย 2. ใช้อัตราป้อนสูงเกินไป 3. ปริมาณของน้ำหล่อเย็นไม่เพียงพอ | 1. ลับคมตัดให้ถูกต้อง 2. ใช้อัตราป้อนให้ต่ำลง 3. เพิ่มปริมาณของน้ำหล่อเย็นในการไล่เศษ |
ความเที่ยงตรงของตำแหน่งรูเจาะ ค่าความกลม ค่าความหยาบผิว ผิดพลาด | 1. ดอกสว่านมีร่องคลายเศษยาวเกินไป 2. สภาพการเจาะแย่ 3. ใช้อัตราการป้อนตอนเริ่มเจาะสูงเกินไป 4. หัวจับดอกสว่านไม่ร่วมศูนย์มากเกินไป | 1. ใช้ดอกสว่านที่มีร่องคลายเศษสั้นลง 2. ลบสันคมจิกแบบ Thinning X-shaped 3. ลดอัตราการป้อนในขณะเริ่มเจาะ 4. ใช้เครื่องมือที่มีค่าการร่วมศูนย์ที่ต่ำลง |
รูเจาะเลื้อย Bent Hole, Un-Straight Hole | 1. ความผิดพลาดของสันคมจิกที่ไม่ร่วมศูนย์, – ความสูงของคมตัดไม่เท่ากัน – ค่ามุมจิกน้อยเกินไป – การสึกหรอของคมตัด 2. ดอกสว่านโก่งงอ 3. ดอกสว่านไม่แข็งแรง 4. เจาะรูบนพื้นเอียง | 1. ลับคมตัดให้ถูกต้อง 2. ตรวจสอบความเรียบร้อยของหัวจับ ปลอก Sleeves ใช้การเจาะ 3. เลือกดอกสว่านที่มีความยาวคมเลื้อยสั้นที่สุด และจับดอกสว่านให้สั้นลง 4. ใช้ปลอกนำเจาะและทำผิวนำเจาะ |
เกิดครีบขนาดใหญ่ที่ปากรูเจาะทะลุ | 1. ลบคมสันคมตัดมากไป (Large Cutting Edge Honing) 2. ใช้ความเร็วป้อนสูงเกินไป ในขณะที่ดอกสว่านกำลังจะทะลุ | 1. ลดขนาดการลบคมที่สันคมตัดให้น้อยลง 2. ลดความเร็วป้อนลง ในขณะที่กำลังเจาะทะลุ |
เศษยาวเกินไป | 1. ใช้อัตราป้อนต่ำไป 2. ภาวะการเจาะแย่ | 1. ใช้อัตราการป้อนที่เหมาะสม 2. ใช้ดอกสว่านที่มีรูน้ำหล่อเย็นภายใน 3. ปรับปรุงจังหวะในการป้อนแต่ละช่วงของการเจาะ |
ดอกสว่านหัก | 1. ความยาวร่องเลื้อยมากเกินไป 2. อัตราความเร็วป้อนมากเกินไป 3. หัวจับมีค่าหนีศูนย์มาก | 1. เครื่องใช้ดอกสว่านที่มีความยาวของร่องเลื้อยที่สั้นลง 2. ลดอัตราความเร็วป้อนลง 3. เปลี่ยนไปใช้หัวจับที่มีค่าการหนีศูนย์ที่น้อยลง |
เกิดการสั่นในระหว่างการเจาะ | 1. มุมหลบของสว่านมากเกินไป 2. ดอกสว่านไม่แข็งแรงเพียงพอ 3. เครื่องจักรและหัวจับสว่านไม่แข็งแรง | 1. ลับคมดอกสว่านให้ถูกต้อง 2. ใช้สว่านที่มีคมเลื้อยสั้นและจับสว่านให้สั้นที่สุด 3. เปลี่ยนไปใช้เครื่องจักรและหัวจับที่แข็งแรงกว่า |
การบิ่นแตกที่ขอบนอกของคมตัด | 1. อัตราป้อนในขณะที่สว่านเจาะทะลุเร็วเกินไป 2. หัวจับมีค่าหนีศูนย์มาก | 1. ลดอัตราป้อนในขณะที่สว่านเจาะทะลุ 2. ใช้หัวจับที่มีค่าการหนีศูนย์น้อยลง |
สันมุมจิกบิ่นแตก | 1. สันมุมจิกยาวไป 2. เริ่มเจาะได้แย่ หนักเกินไป | 1. ลดความยาวของสันมุมจิก 2. ลดความเร็วป้อนลงเมื่อเริ่มเจาะ |
การสึกหรอขนาดใหญ่ที่ขอบนอกของคมตัดและสันคมเลื้อย | 1. ใช้ความเร็วตัดสูงเกินไป 2. เกิดความร้อนสูงในการตัดเฉือน ในจุดของบริเวณที่กำลังเจาะ | 1. ลดความเร็วตัดลง 2. ใช้ดอกสว่านที่มีรูน้ำอยู่ภายใน |
ลิ่มของด้ามจับหัก | 1. ผิวของด้านจับเป็นรอย 2. ปลอกหัวจับเป็นรอยและสึกหรอ | 1. ลบรอยขีดข่วน สิ่งสกปรก และครีปที่เกิดขึ้น 2. เปลี่ยนปลอกหัวจับใหม่ |